ALPOLIC™ NC/A1 meets testing requirements as a DtS non-combustible cladding for Project Remediate
ALPOLIC™ NC/A1 ticked all the boxes and passed all CPSP testing criteria to be approved for Project Remediate. Learn more about the process here.
Combustible cladding materials have become a significant challenge for the construction industry in recent years resulting in the search for alternative non-combustible cladding solutions.
After several incidents involving combustible cladding in residential buildings, both here in Australia and overseas, the demand for a non-combustible, fully compliant cladding material has increased exponentially. All industry stakeholders now want a way to improve the integrity of a building whilst also ensuring the safety of the occupants inside.
Because of this, the NSW Government has worked to establish a key oversight panel for this matter, as well as a funding program, titled Project Remediate, to assist building owners that are required to replace combustible cladding on their residential buildings.
Project Remediate and the Cladding Product Safety Panel (CPSP)
In 2020, the NSW Government commissioned the Cladding Product Safety Panel (CPSP) to provide expert advice to the NSW Cladding Taskforce and the Cladding Support Unit on the suitability of cladding replacement products and wall assembly methods.
At the same time, the NSW Government also established Project Remediate, a funding scheme designed to provide the owners of Class 2 residential apartment buildings in NSW with a 10-year interest-free loan and an assurance service for the remediation of combustible cladding on their residential buildings with CPSP-approved materials.
In April 2021, the CPSP released their first report on non-combustible material alternatives. At the time, they outlined four materials that they had deemed suitable replacements for combustible cladding. While Bonded Laminate Material (BLMs) was not one of these initially approved materials, the CPSP noted that they would give further consideration to BLMs moving forward.
This culminated in the release of additional testing criteria for BLMs just a few months later.
The CPSP’s additional testing criteria for BLMs
In November 2021, as part of an industry briefing, the CPSP announced the following criteria that would be used as additional testing on Bonded Laminate Materials for fire safety and compliance:
- Tests to be conducted on two representative types of BLM:
- Aluminium skin – mineral core
- Aluminium skin – aluminium core
- Testing will include joints and penetrations
- BLM (as a whole assembly) will be tested to determine spread-of-flame and smoke development as per AS/NZS 1530.3
The tests for spread-of-flame and smoke-developed indices will be conducted on the front and back of each of the two representative materials:
- BLM with no perforations and no joints
- BLM with electrical cable-sized perforation (20mm x 20mm)
- BLM with bathroom exhaust-sized perforation (200mm x 200mm)
- BLM prepared with intersecting horizontal and vertical joints
As part of this testing phase, Network Architectural’s ALPOLIC™ NC/A1 DtS non-combustible cladding was one of two BLM products that were selected to be tested. This phase took close to 5 months to complete, and results were released soon after.
This image is an extract from the CSIRO’s Advisory Report on Additional Testing for ALPOLIC™ NC. View full report.
The final results of the CPSP’s BLM testing
In April 2022, the CPSP released their second report, providing an update on the additional replacement cladding materials that had now been approved for use in Project Remediate.
After undertaking the testing specifications for the purpose of meeting CPSP Report 2 requirements, Network Architectural was extremely pleased to find that our BLM product, ALPOLIC™ NC/A1, had ticked all the boxes and passed all necessary testing criteria to be approved for use in the Project Remediate program.
For more, see Press Release: ALPOLIC™ NC/A1 satisfies all testing requirements for NSW Government’s Project Remediate recladding scheme
This means that not only does our DtS non-combustible cladding meet all Australian Standards set out by the National Construction Code (NCC), but it now also meets the additional fire testing safety criteria which has been made mandatory by the CPSP to be considered for use as a replacement for dangerous, flammable cladding under Project Remediate.
Further evidence of the suitability of Bonded Laminate Materials (BLM) as replacement products for Project Remediate can be found in the recently released NSW Government’s Project Remediate Cladding Replacement Pattern Book. Click to download your copy below.
So, whether you’re already registered for Project Remediate or you’re simply looking for the world’s safest, most tested facade material for your next construction project, you can now feel safe in the knowledge that the ALPOLIC™ NC/A1 has been thoroughly tested and approved by the NSW Government.
This image is an extract from the CSIRO’s Advisory Report on Additional Testing for ALPOLIC™ NC. View full report.
Are you looking for compliant, fire-safe cladding for your next construction project?
Network Architectural is your trusted partner for innovative facades and ceilings.
Our ALPOLIC™ NC/A1 fire-safe aluminium composite cladding takes fire protection to the next level. With a non-combustible mineral core containing zero polyethylene, our fully compliant material is far superior to other aluminium cladding alternatives on the market.
Plus, with ALPOLIC™ by Mitsubishi Chemical Infratec Co., Ltd’s 20-year unconditional full rectification cover manufacturer’s warranty, you’ll have total peace of mind using the world’s most successfully tested and safest aluminium facade material available today.
Additional benefits of ALPOLIC™ NC/A1
ALPOLIC™ NC/A1 has an A1 rating under European testing and is also vastly superior to outdated (solid aluminium) products in terms of environmental sustainability with 500 times better thermal conductivity, a higher energy rating and an Environmental Product Declaration (EPD) produced by GECA.
ALPOLIC™ NC/A1 also provides superior flatness and is not susceptible to ‘oil-canning’, an inherent property of solid aluminium. Oil canning is the rippling of metal cladding caused by thermal expansion due to heat. It causes unsatisfactory aesthetics and stress on the structural integrity of the system that is not permitted under Project Remediate guidelines and can lead to a defect notice.
Available from Network Architectural, ALPOLIC™ NC/A1 comes in a large selection of colours and finishes, and has an industry-leading 20-year warranty. It has superior durability and impact resistance, and comes standard with Lumiflon FEVE paint technology, making it highly resistant to weathering, UV radiation, corrosion and colour fading.
Learn more about ALPOLIC™ NC/A1
If you would like to learn more about ALPOLIC™ NC/A1, contact us today on (02) 8316 5000 or visit our website here.
Our team of architectural cladding and building supplies experts will be happy to help.
Related Articles
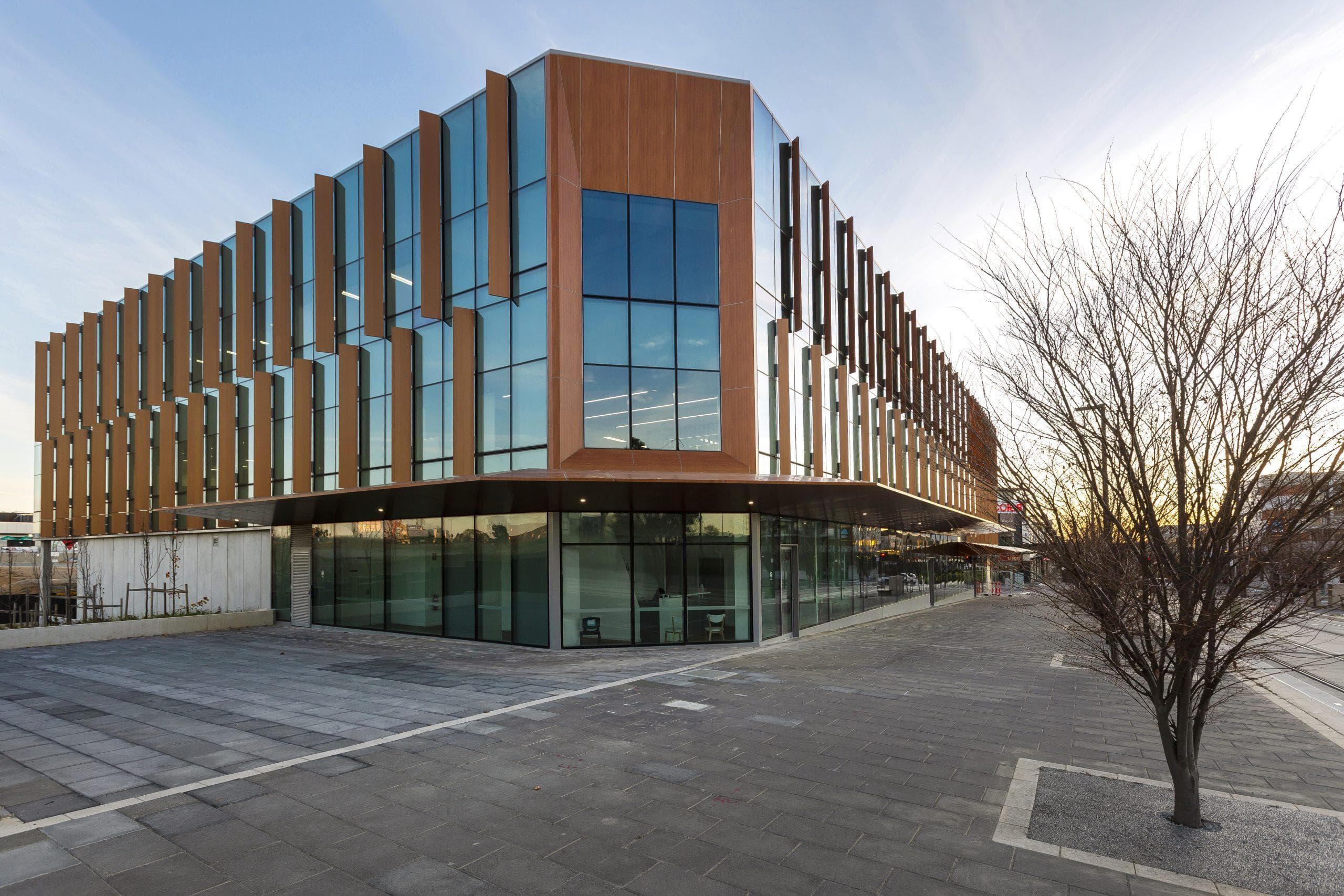
Engineering Resilient Facades
Australia’s extreme climate demands durable facades that ensure safety, performance, and longevity. This whitepaper explores key compliance standards and material solutions, designed to withstand harsh weather and thermal expansion.
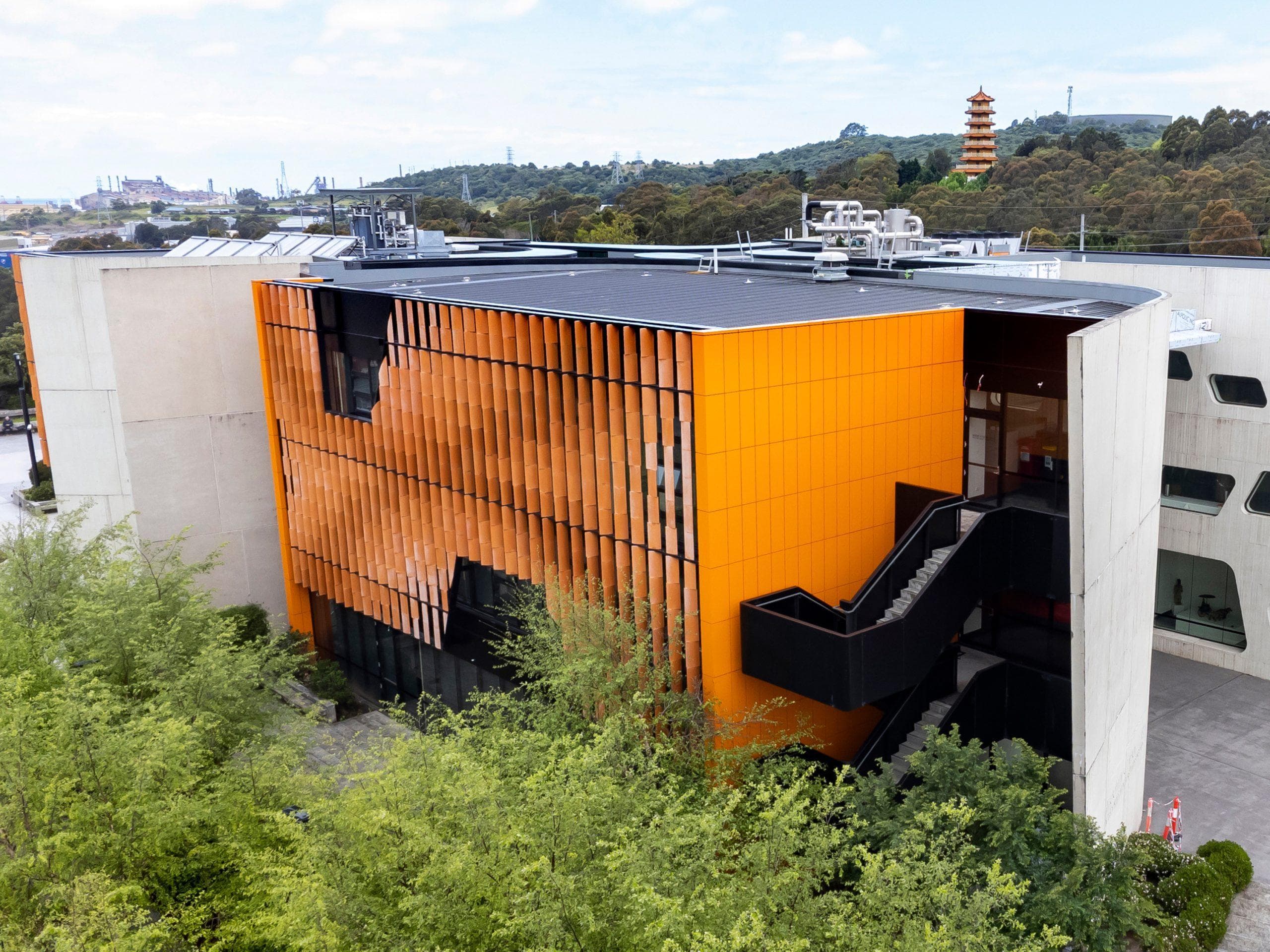
Sustainability eBook 2024
For the third year in a row, Network Architectural was proud to sponsor the Commercial Architecture (Large) category for Architecture & Design’s Sustainability Awards 2024.
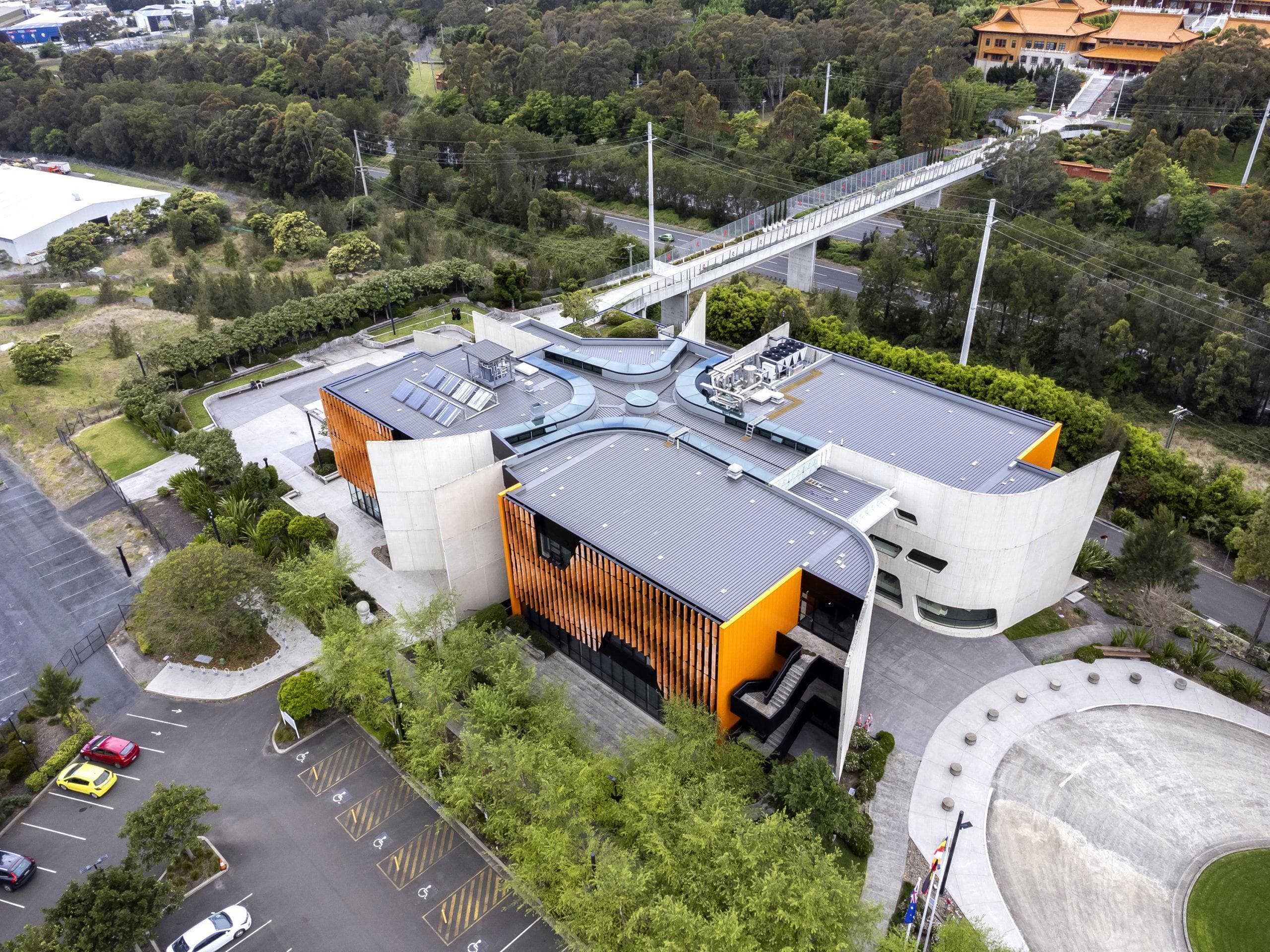
Compliant Non-Combustible Aluminium Recladding at Nan Tien School of Higher Education
Discover how Nan Tien Institute overcame the challenge of non-compliant cladding, achieving full fire safety compliance while enhancing the building’s aesthetics and reducing insurance costs. ALPOLIC™ NC/A1 delivered a seamless blend of durability, sustainability, and style. Read more to uncover the steps behind this remarkable transformation.