Weathering the storm: ALPOLIC’s role in creating resilient architecture for changing climate
Amidst Australia’s climate crisis, ALPOLIC™ panels offer exceptional weather resistance and durability. Tested to meet rigorous standards, these panels withstand extreme conditions while maintaining aesthetic appeal. From the Q1 Tower to the Queensland Children’s Hospital, ALPOLIC™ showcases the resilience and sustainability needed for future-proof architecture.
Remember when weather was merely a topic of casual conversation? Now, amidst the escalating emergency of the climate crisis, it’s a subject fraught with anxiety and uncertainty – especially because Australia is experiencing some of the most pronounced effects of global warming. From scorching heat waves and devastating bushfires to intense rainfall and torrential floods, we have endured a rapid surge in extreme weather events. This fundamental development is radically reshaping the built environment, presenting architects and designers with an urgent challenge: to create buildings that not only withstand these volatile and largely unpredictable conditions, but also contribute to a more sustainable, resilient and – hopefully – more stable future.
As a result, now, more than ever, the choices architects and designers make regarding materials, construction techniques, and overall design strategies are critical, and selecting products that can endure harsh weather conditions, resist corrosion, and offer long-term durability is paramount to ensuring the safety and longevity of the built environment in Australia.
Tried and tested solutions provide confidence for uncertain future
Assessing weatherability during the planning and design phases is crucial to ensure optimal performance and sustainable outcomes throughout a building’s lifecycle, and early collaborative engagement with suppliers who provide comprehensive testing data is absolutely essential.
This includes simulations of various environmental conditions and, ideally, independent certifications demonstrating compliance with relevant standards. As many industry professionals are aware, AS4284 is a crucial Australian standard for evaluating a building facade’s ability to resist water penetration under simulated weather conditions. Additionally, AAMA2605 is a widely recognised North American standard that outlines rigorous testing procedures for assessing the performance of organic coatings on architectural aluminium extrusions and panels, providing valuable insights into their resistance to fading, chalking, and corrosion.
Prioritising materials with proven weather resistance, backed by compliance with standards like AS4284 and AAMA2605, can significantly mitigate the risks associated with extreme weather events. By making informed decisions based on robust testing data and recognised industry standards, architects and builders can create more resilient structures.
ALPOLIC™: A proven solution for a changing climate
Manufactured in Japan by Mitsubishi Chemical Infratec Co., Ltd, ALPOLIC™ exemplifies a superior choice for architects seeking to safeguard buildings against the escalating challenges of Australia’s climate. The panels have been rigorously tested to meet or exceed international standards – including AS4284 for water resistance and AAMA2605 for coating performance, ensuring resilience against corrosion and UV degradation. Plus, the panels have also undergone cyclone testing. Here, we look at specific aspects of ALPOLIC design that ensure its outstanding quality, reliability and weather performance.
First of all, the panels are engineered with high-quality aluminium, which equips them with outstanding structural integrity, and enables them to resist the forces exerted by high winds, heavy rain, or even hail. This endurance in the face of even the most trying conditions is further reinforced by corrosion resistance, UV stability and thermal expansion control. ALPOLIC™’s advanced Lumiflon FEVE paint coating technology ensures that the panels maintain their aesthetic appeal even when exposed to prolonged moisture, salt spray, or acidic pollutants and its high resistance to UV degradation ensures colours don’t fade away. The panels’ one-of-a-kind, mineral-filled core protects the exterior from damage over time, such as denting or oil canning, brought on by Australia’s increasingly severe weather conditions. These characteristics contribute to the panels’ distinctive flat profile and their capacity to retain their shine and lustre for about 50 years.
The iconic Q1 Tower in Queensland stands out as a testament to ALPOLIC™’s incredible weatherability, as the building has been withstanding the harsh conditions of its seaside locale since completion in 2005. Positioned only a couple of hundred metres away from breaking surf and exposed to salt air and Queensland’s unforgiving sun for over 20 years, the building still maintains its structural integrity and aesthetic appeal, with the ALPOLIC™ panels installed across its exterior still looking as good as they did when first installed.
Designed by Conrad Gargett and Lyons, the Queensland Children’s Hospital is another example of ALPOLIC™’s resilience. Completed exactly a decade ago, the hospital’s exterior remains vibrant despite Brisbane’s unrelenting tropical heat, humidity and intense sun exposure. Here, 55,000m² of the ALPOLIC™ product in various custom colours including vivid green, turquoise and purple were used on the building’s exterior louvres and protruding components to achieve the architects’ engaging and immersive vision – and thanks to ALPOLIC’s Lumiflon FEVE resin technology, the panels still look like they did on the day of installation.
These pristine facades highlight the panels’ exceptional resistance to heat. ALPOLIC™ products are engineered to minimise thermal expansion and contraction, preventing warping, buckling, or cracking – an essential consideration when specifying materials in areas set to experience extreme temperature variations.
Reliable fire performance is another quality making ALPOLIC™ NC/A1 particularly suited for an increasingly volatile, harsh climate. The mineral core of ALPOLIC™ NC/A1 is non-combustible, preventing it from catching fire even when exposed to high temperatures – a quality particularly relevant in bushfire-prone areas. In fact, it has been tested and certified to meet the Euroclass A1 standard, the highest possible rating for non-combustibility. That means the panel has passed rigorous tests simulating real-life fire scenarios and has shown no propagation nor spread of flame.
ALPOLIC™’s exceptional durability and weather resistance ensure reliability and longevity in the face of escalating extreme weather events. In that, they also offer additional benefits that reinforce ALPOLIC™ as a particularly sustainable choice for an uncertain future. Durability and structural integrity minimise maintenance and replacement requirements, which minimises costs, need for additional resources and labour, associated transportation and logistics, construction waste, and – as a result – the building’s environmental impact is vastly reduced. In addition, in contrast to other products which might require cleaning up to four times a year, ALPOLIC™ panels do not require cleaning to maintain their warranty at all – which only reduces their environmental impact further. Plus, the availability of an Environmental Product Declaration (EPD) for the panels provides clarity about their environmental impact throughout their life cycle, fostering transparency and informed decision-making for sustainable building design.
In a world grappling with the increasing urgency of climate change and more unpredictable, volatile weather patterns, the architectural community is bound to play a vital role in creating a resilient built environment that can endure and thrive. By prioritising weather-resilient design and specifying meticulously tested high-performance materials and products like ALPOLIC™, architects, designers and construction professionals can help create sustainable and resilient buildings – and a greener, more stable future for Australia.
Related Articles
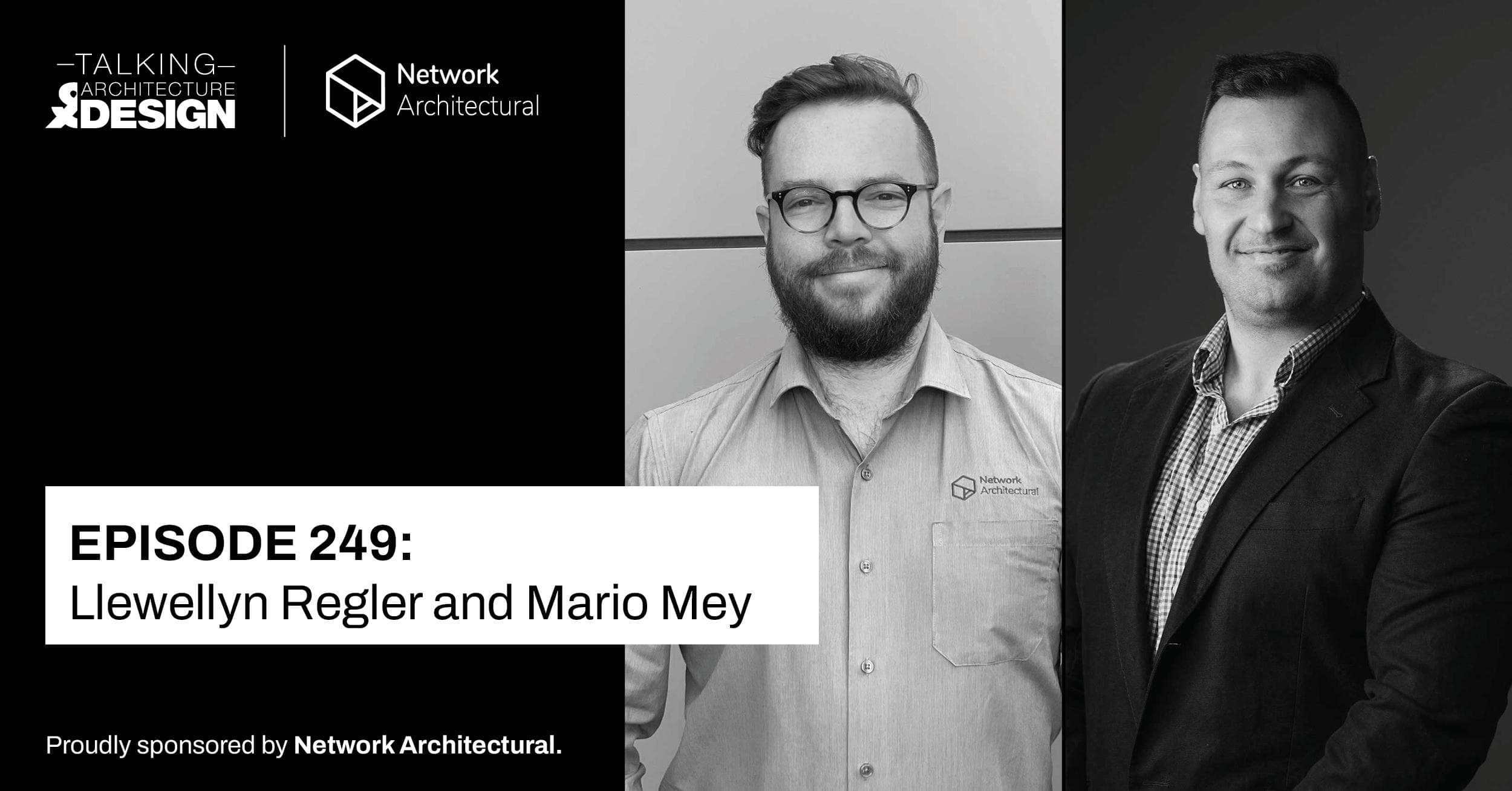
The Cladding Conversation: Facade Engineers Shouldn’t be an Afterthought
In this episode of Talking Architecture & Design, Total Building Engineering Solutions’ Mario Mey and Network Architectural’s Llewellyn Regler explore why engaging Facade Engineers early in a project is essential—not optional. From fire safety and waterproofing to the benefits of using ALPOLIC™ cladding, they discuss the evolving cladding landscape, the impact of the DBP Act, and the future of safe, high-performing facades.
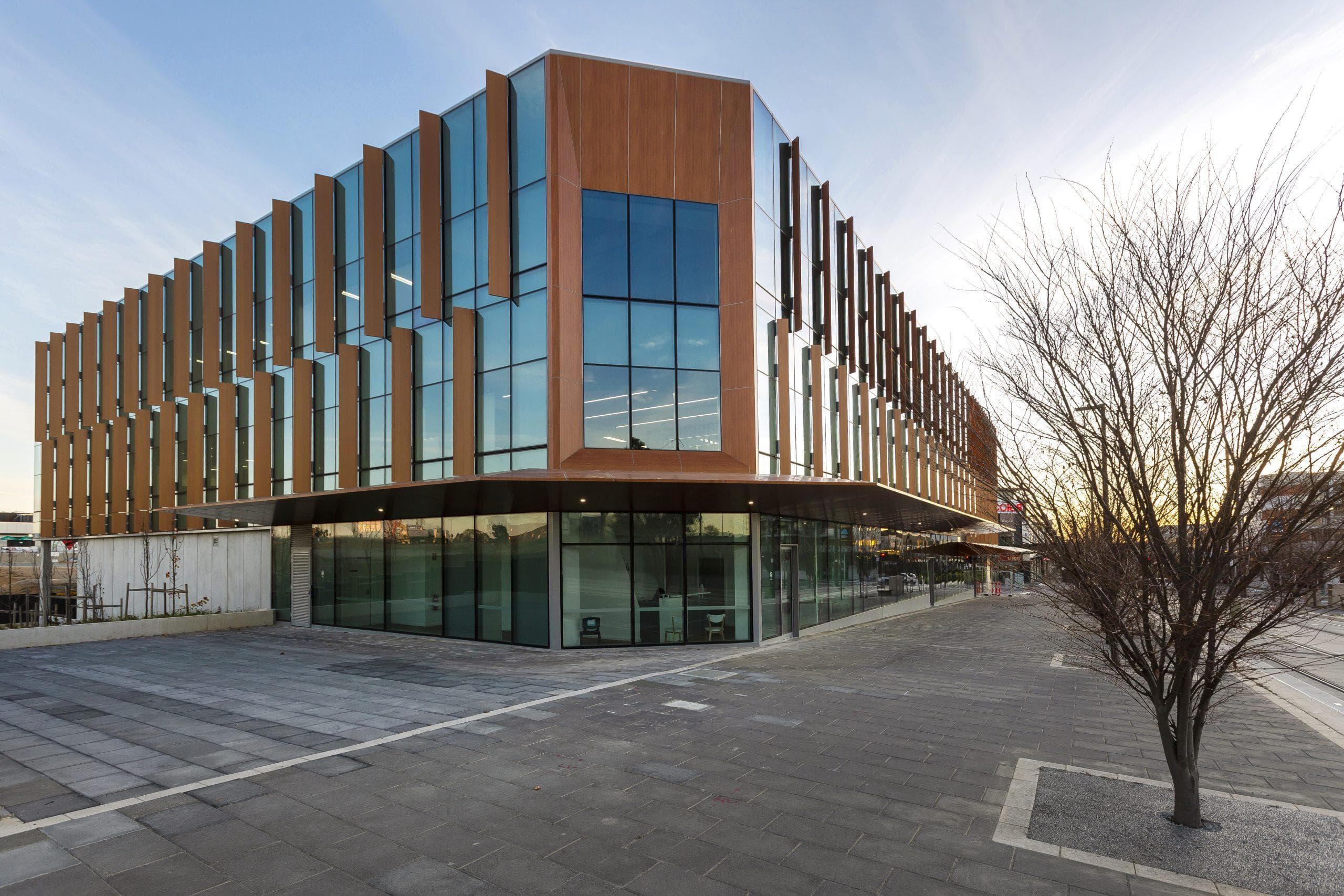
Engineering Resilient Facades
Australia’s extreme climate demands durable facades that ensure safety, performance, and longevity. This whitepaper explores key compliance standards and material solutions, designed to withstand harsh weather and thermal expansion.
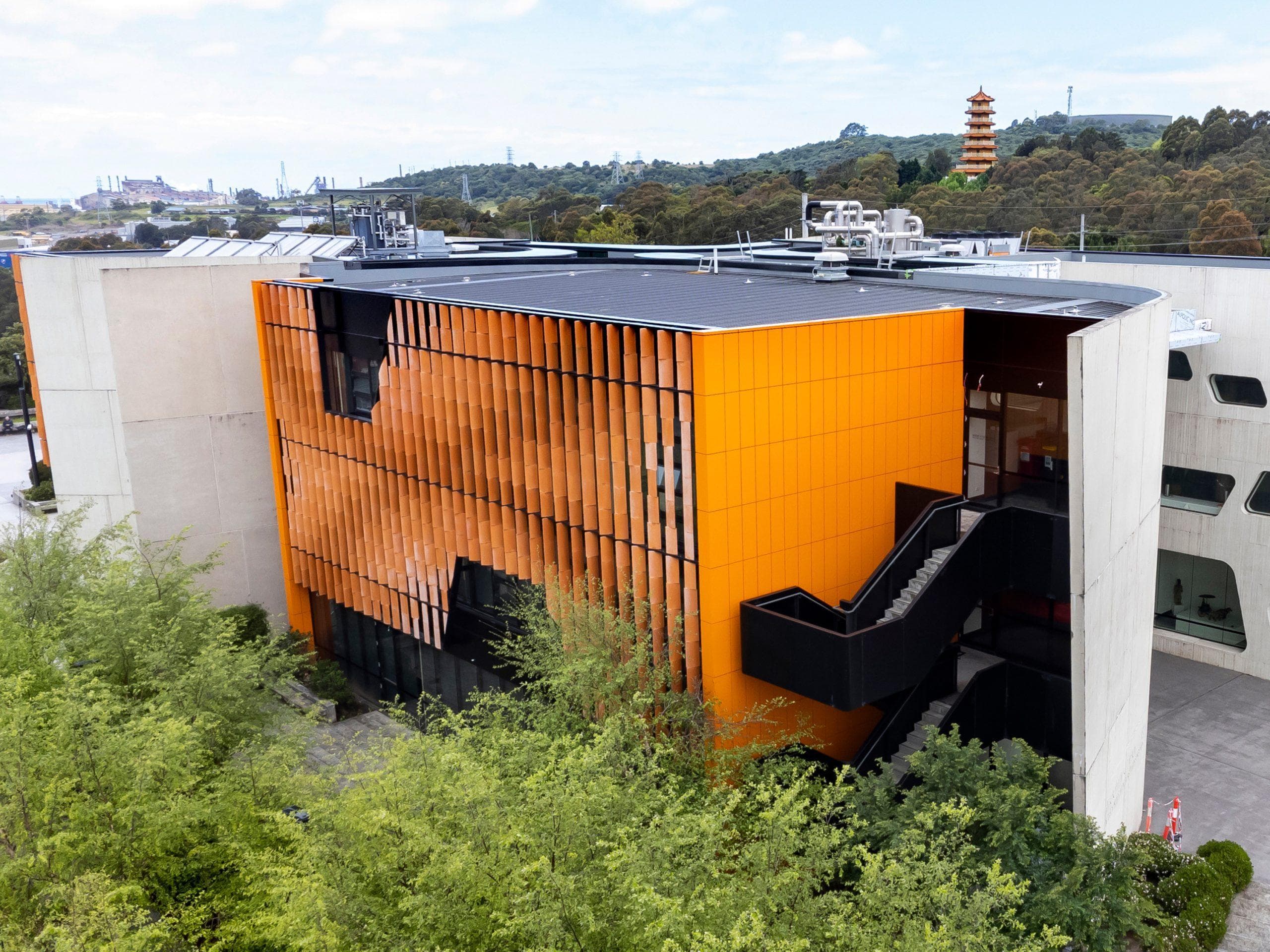
Sustainability eBook 2024
For the third year in a row, Network Architectural was proud to sponsor the Commercial Architecture (Large) category for Architecture & Design’s Sustainability Awards 2024.